

- #BOSCH IBOOSTER AND COMPUTER GENERATOR#
- #BOSCH IBOOSTER AND COMPUTER DRIVER#
- #BOSCH IBOOSTER AND COMPUTER SOFTWARE#
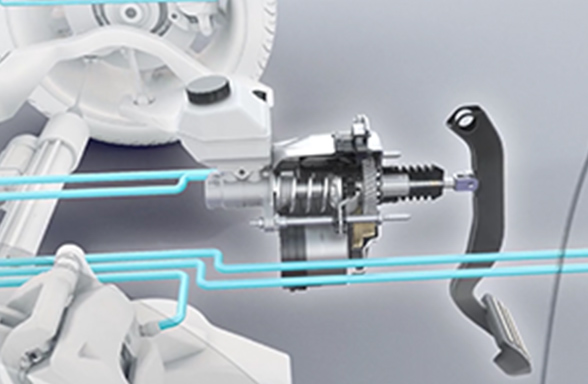
Using intelligent mathematical models, PPC is able to achieve impressive precision while taking into account environmental factors. air bubbles, ambient temperature) are used for feed-forward control in highly dynamic operation and for diagnosing leakages for example. Characteristic maps for displaying environmental factors (e.g. Core elements of PPC are the phase current sensor, the angular sensor detecting the rotor position of the EC motor and adaptive characteristic maps. Braking pressure is built up through the forward movement of the piston and through the shifting of hydraulic fluid (pressure), and is reduced in a highly dynamic fashion by the return motion of the piston (pressure release). PPC is the core concept of the high-precision braking pressure regulator ( E87DE-SA, E87DE-TA1, E90DE-SA) using a brushless electric motor and a piston-cylinder unit. The ABS function and the noise level on snow, ice and µ-split were even improved, which in turn defined a new benchmark for brake control in critical driving situations. Brake pressure control was thus possible for the first time through current control of the electric motor, which is a core component of today's redundancy functions. The signals of the current of the electric motor, the piston position and the pressure in the piston-cylinder unit were essential components in the modeling process. At the core of this precision pressure control was both a highly accurate position and speed regulation of the piston using a three-phase brushless electric motor as well as a very precise modeling of the relationship between braking torque, brake pressure and electric motor torque.
#BOSCH IBOOSTER AND COMPUTER GENERATOR#
System pressure could now be modified independently of pedal actuation, and regulated or controlled with the utmost precision, all taking into account the braking effect of a generator or of the recuperative electric motor of an electric vehicle. On top of that, fully variable pedal characteristics could be achieved.
#BOSCH IBOOSTER AND COMPUTER DRIVER#
A pedal feel simulator made it possible to completely decouple the driver from the system pressure of the brakes, which then laid the foundation for the first autonomous driving functions such as automatic electric emergency braking (AEB). This was made possible by generating brake pressure through a piston-cylinder system driven by a brushless electric motor and distributing it to several wheel brakes via solenoid valves. speaking and self-driving Pontiac Firebird replica at its booth on display.IBS1 represented the world premiere of a brake-by-wire system that combined the functions of brake actuation, brake boosting and ABS/ESC, including initial autonomous driving functions ( AEB - Automatic Emergency Braking) as well as featuring recuperative braking with generators – all in one single compact unit.īoth, the compact design of the brake system and the precision of the brake pressure control by an electro-hydraulic system was revolutionary – and unimaginable at the time. To illustrate its commitment to self-driving cars at CES, Bosh had a Knight Rider, K.I.T.T.
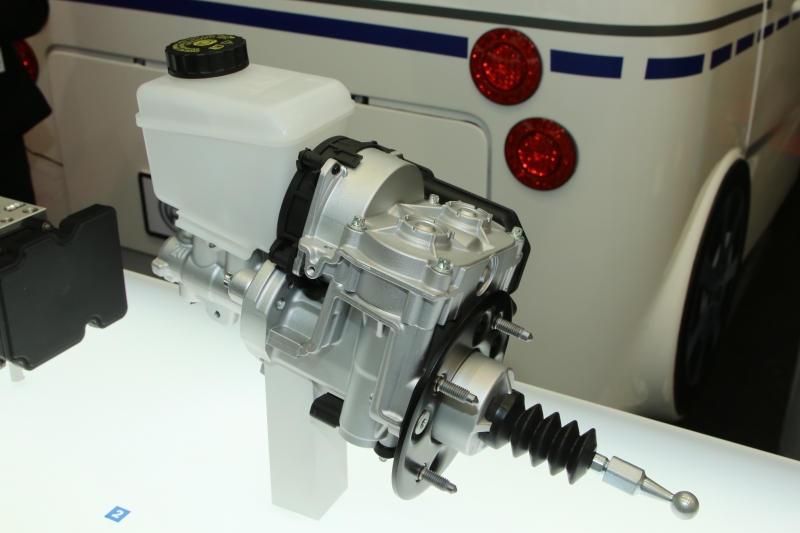
There were major autonomous vehicle announcements from Mercedes-Benz, Audi and BMW…all German engineered cars. The iBooster are used in EVs in most typical traffic delays it can be used to recover maximum braking energy for the hybrid or electric vehicle’s electric motor.īosch supplies the electric motor and long-range radar for the Google self-driving car. The iBooster can also provide the gentle braking required by the ACC adaptive cruise control, all the way down to a complete stop, while being almost silent. Both iBooster and the ESP braking control system are designed to brake the car – independently of each other – without the driver having to intervene. Bosch already has a fall-back for brakes: the iBooster, an electromechanical brake booster.
#BOSCH IBOOSTER AND COMPUTER SOFTWARE#
Powerful software and computers process the collected information and ensure that the automated vehicle can move through traffic in a way that is both safe and fuel efficient.Īs vehicles gradually take over more and more driving tasks, safety-critical systems such as brakes and steering must satisfy special requirements.īosch notes that if one of these components fail, a fall-back is needed to ensure maximum availability. It is based on sensors featuring radar, video, and ultrasound technology, sensors Bosch has been manufacturing by the millions for many years. Automated driving affects every aspect of the car – powertrain, brakes, steering – and requires comprehensive systems expertise.
